US: How Are Wind Turbines Made?
- Citizens' Platform
- Feb 3, 2023
- 4 min read
Source: Union of Concerned Scientists
Many humans feel at least a bit of “megalophilia”—a love of very, very big things. This might be one of the many reasons why wind turbines fascinate us. Imagine the dazzling dizziness of looking up at the world’s tallest wind turbine: the Max Bögl Wind AG turbine in Germany stands 808 feet tall—the height of two and a half Statues of Liberty.
Wind turbines aren’t just big towers. They are big opportunities for achieving a 100 percent clean energy future. In 2021, US wind power reached a generating capacity of 136 gigawatts (GW) and supplied 9 percent of all US electricity generation. That’s enough to power 39 million homes.
According to the US Department of Energy (DOE), wind provides more than 10 percent of electricity generation in sixteen states—and more than 30 percent in five states (Iowa, Kansas, Oklahoma, South Dakota, and North Dakota). While almost all this US wind power currently comes from land-based (“onshore”) wind turbines, the Biden administration is aiming to reach 30 GW of offshore wind capacity by 2030, and 15 GW from floating offshore wind technology by 2035. Offshore wind turbines can be larger with greater generating capacity, and wind speeds tend to be more consistent and faster at sea.
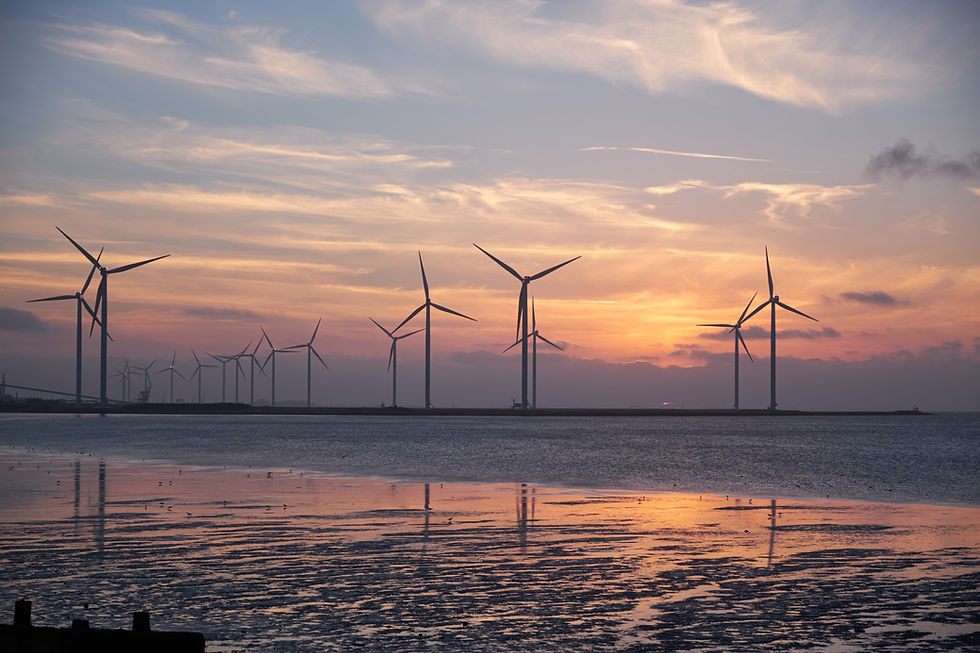
So, just how are these tyrannosaurus turbines, these momentous machines, made?
Building from the ground, or seabed, up
According to DOE’s Wind Energy Technologies Office, a typical large-sized wind turbine contains about 8,000 parts within its foundation, tower, nacelle, and blades. There are over 500 facilities manufacturing wind turbine components in the US.
The foundation: Once developers select a site for a land-based turbine tower, they level the ground and lay down a concrete foundation, which can use as much as 600-1000 tons of concrete and 165 tons of steel.
Installing an offshore wind turbine foundation, on the other hand, is a different story. Honestly, it is nothing short of epic. Huge ships leave port and arrive at a site that’s up to 200 feet deep. The ships then plant down legs to root it to the seabed and elevate the ship out of the water. Next, an onboard crane lowers a steel tower “monopile” (or, depending on the site, a different anchoring structure such as a jacket, tripod, or gravity base) into the water and drills it into the sea floor. A crane places a transition piece above the monopile or anchored foundation, on which the tower will be secured with cables. For deeper floating offshore wind turbines, extending down 200 feet or more, wind turbines are placed atop buoyant substructures at port facilities and towed to their location where mooring lines connect the structure to anchors rooted into the seabed.
The tower: For onshore wind, trucks bring in the steel components of the tower and it is assembled on site with the tower lying horizontally on the ground. The average US tower height (or “hub” height, measured from the base to the center of the blades) in 2021 was 300 feet, 66% higher than in 1999. By 2035, the average onshore American wind turbine tower is projected to reach about 500 feet. When ready to be erected, a crane pulls the tower upright.
For offshore wind, large boats transport the pre-assembled steel tower to the foundation. Crane operators on the ship’s deck remotely guide the towers into position on top of the transition piece.
The nacelle: The electrical box at the center of the blades is known as the nacelle. Made of fiberglass, the nacelle houses the gearbox, generator, and electronic systems for each wind turbine. In both onshore and offshore wind turbines, a crane lifts the nacelle onto the top of the tower. Inside the nacelle is either an induction generator or a permanent magnet generator (PMG). Despite their higher upfront costs, 36% of onshore and 76% of offshore wind turbines use PMGs because they are more efficient for larger turbines. Also, because they do not require a gearbox, PMGs are quieter and need less maintenance. PMGs are made using a combination of the rare earth elements neodymium, praseodymium, dysprosium, and terbium.
The blades: The part you’ve been waiting for! Blades are getting bigger and better each year, with an average rotor diameter (the size of the full blade circle) of 418 feet in 2021. That’s 164% bigger than in 1999. Average 2021 US wind turbine capacity was 319% higher than in 1999. Manufacturing processes continue to evolve towards larger, more efficient, and longer-lasting blades.
Let’s simplify the complex process of making a wind turbine blade by thinking about it like a sandwich. We start with the bread, a large blade-shaped mold filled with dry fibers. Next, we toast it: we inject a resin into the fibers, it fills all the air pockets between the fibers, then we heat it to produce hardened carbon fiber. Running along the length of the blade, a carbon “spar,” or spine, is added for rigidity and strength.
Curved balsa wood, foam, or recycled plastic is added as the next layer. These materials are like lettuce; they add strength without adding much weight. More dry fibers are added on top of the sandwich (yum!) and another resin is injected through them (mayo) with air-tight vacuum suction bonding it into the fibers. Next, strong supports called webs are erected upright within the mold, which will act as a supportive brace within the hollow center of the blade. On top of our open-faced sandwich, the top half of the blade (produced via an identical process) is folded over and secured. That is the biggest, most green sandwich anyone has ever made.
Fun fact: some wind turbine blades take two days and 100 employees to manufacture!
Once the blades are delivered to the site, huge cranes directed by computer-assisted operators carefully guide the three blades into the nacelle. Whoosh! We’re spinning on renewable energy. Wind energy is already running circles around its fossil fuel competitors, as the price of wind energy gets cheaper and cheaper compared to coal and gas.
Comments